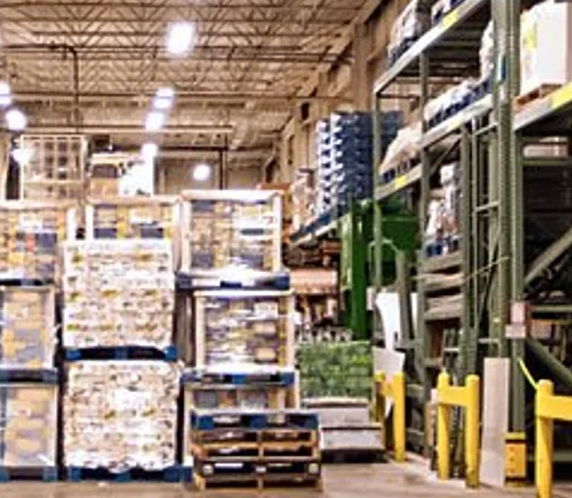
Advancing Industries through Rotational Molding
Have you been between those hearing a good deal about Rotational Molding or Rotomolding but don’t have got a very clear comprehension of what it is? Look no further than this comprehensive information, when we will require you through this process, historical past, resources, pros, and uses of rotational molding in depth.
Plastics Rotomolding, also called Rotomolding, is a manufacturing procedure employed to develop hollow plastic-type pieces. This process is proper for making huge, sophisticated, or smooth components that would be tough to generate employing other producing functions. Let us explore Rotomolding in depth.
History of Rotational Molding
Rotational molding traces its beginning to the 1940s in The european countries, where it was initially hired to help make dolls and newborn playthings. In the 1950s, a couple of companies created kayak car seats by using this method, and also over time that it evolved into generating larger sized and a lot more complex elements.
Rotational Molding Process
Rotomolding is actually a four-stage process. Very first, the natural substance in natural powder develop is jam-packed right into a mildew, along with the mildew is covered. Second, the mildew is warmed up and rotated horizontally or vertically around two perpendicular axes. Third, the material melts and layers the inside in the mold. Ultimately, the mildew cools, and the part is ejected.
Supplies Utilized in Rotational Molding
Polyethylene (PE) is regarded as the widely used substance in Rotomolding due to the price-usefulness, impact resistance, and adaptability. Many other materials like Nylon, Polypropylene, Polycarbonate and Pvc material can also be used depending on the application and attributes necessary.
Features of Rotational Molding
Rotational molding delivers several advantages such as:
(i) Expense-efficiency: Rotomolding provides faster manufacturing period occasions, which means decreased work costs, tooling costs, and routine instances.
(ii) Design and style Versatility: Rotomolding can create intricate, smooth, or multiple-layered pieces, making it an excellent procedure for customized components patterns.
(iii) Sturdiness: The parts generated via Rotomolding are durable, deterioration-proof, and resistant to weathering and UV radiation.
Uses of Rotational Molding
Rotomolded elements are used in a variety of businesses and apps, which includes automotive, agriculture, development, and leisure time gear. Common Rotomolded goods consist of water tanks, gas tanks, playground equipment, boxes, and kayaks.
Summary:
Rotational molding, also known as Rotomolding, is a procedure that has been around for years and has demonstrated to be incredibly adaptable, offering many pros over other production strategies. In this particular extensive guideline, we now have demystified the Rotomolding approach, historical past, materials used, benefits, and software. Understanding the fundamentals of Rotomolding will help you determine whether it’s the correct developing method for your next undertaking.