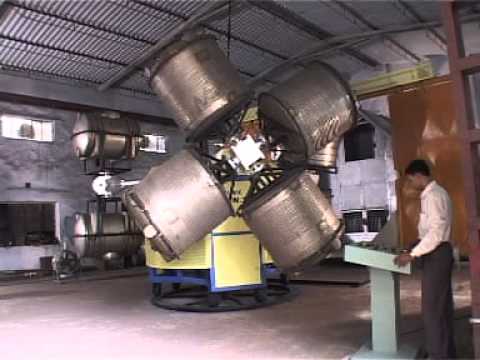
Analyzing Mold Design to Enhance Part Quality in Rotomolding
Rotational molding is surely an incredibly flexible plastic material fabrication approach which can be used to create great-high quality parts and components for many different sectors. This procedure requires placing a powder or fluid plastic-type material in a mold, which is then rotated in order to uniformly deliver the information. The temperature and push created by the rotation helps to form and make up the portion as wanted. In the following paragraphs, we shall get a closer inspection at Rotational Molding as well as its several apps.
How Rotational Molding Works
Rotational molding starts with raw Plastics Rotomolding either in powder or liquefied type. The natural powder or liquefied is put right into a metal, pass away-cast light weight aluminum, or steel mold that has been heated up to temperatures between 200°F and 500°F qualifications. Then, the mold is rotated on two axes while simply being warmed up in order that the resin inside equally distributes through the complete cavity in the mold. This produces even walls thicknesses during the entire concluded merchandise which boosts its durability and strength.
Some great benefits of Rotational Molding
Rotational molding gives many distinctive positive aspects over other forms of plastic manufacturing procedures for example shot molding or blow molding. First of all, rotomolding is quite a bit faster than traditional methods simply because it relies upon gravity and centrifugal pushes instead of pressure to fill the molds. Furthermore, this developing process also provides for sophisticated styles and fashions that happen to be challenging to obtain using other approaches for its ability to generate 1-piece components with sophisticated specifics like figure and easy transitions between distinct sections of the aspect. Additionally, rotomolding also makes items with steady wall thicknesses causing them to be more powerful and more resilient compared to those made with many other functions. Ultimately, as there are no razor-sharp sides or edges when working with rotomolding, it is ideal for creating little one-safe items including playthings and playground gear without having to sacrifice any high quality in layout or design.
Conclusion:
As you can tell from my guide previously mentioned, rotational molding is surely an incredibly functional manufacturing procedure that offers numerous advantages over standard manufacturing approaches including injection molding or blow molding. Furthermore it allow for intricate forms with regular wall structure thicknesses but it also operates rapidly while generating safe products which are resilient enough for years of usage with small servicing necessary. If you’re searching for a strategy to create great-high quality components swiftly without having to sacrifice any top quality within your design then rotomolding might be just the thing you’ve been looking for! Having its several advantages over standard producing operations, it’s easy to see why this procedure is becoming so popular among businesses sizeable and tiny alike – why not give it a go?